项目概述
1. 生产计划
600套/天(117/118轴承座)
2. 加工线要求:
1)适用于自动生产线的数控加工中心;
2)液压工装夹具;
3)自动上下料装置及输送装置;
4)总体加工工艺及加工周期;
生产线布局
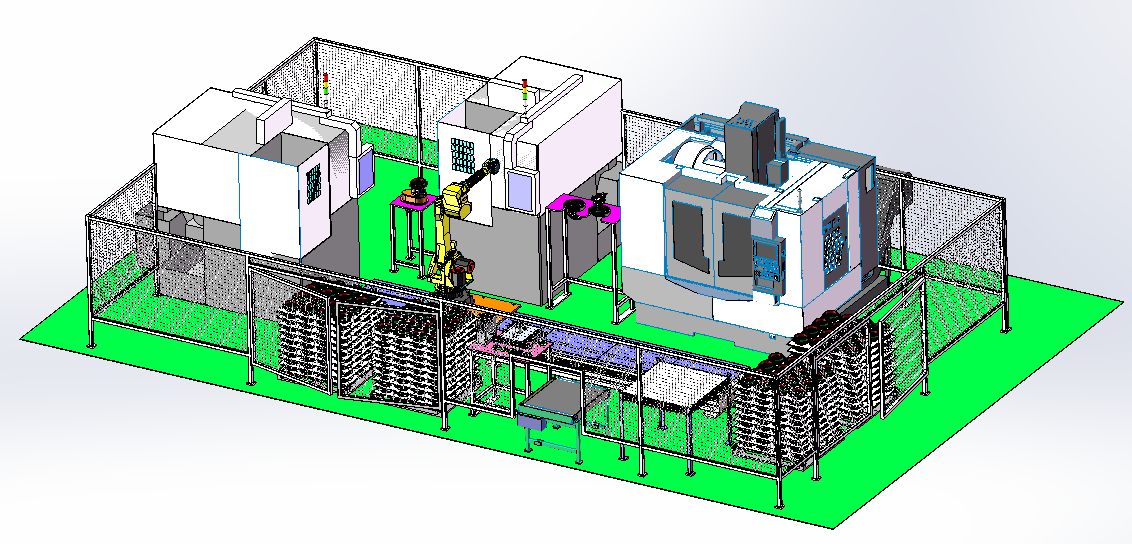
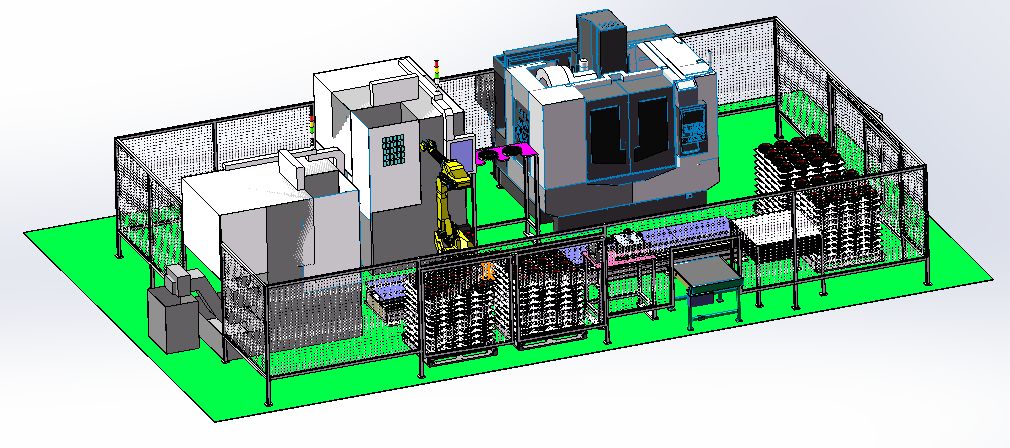
生产线布局
机器人动作介绍:
1、将粗加工、摆放好的篮子手动放置在载物台上(1号载物台、2号载物台),并按键确认;
2、机器人移动到1号上料台的托盘处,打开视觉系统,抓取A、B零件并分别移动到角度观察站等待上料指令;
3、角度识别工位发出上料指令,机器人将1号工件放入转盘定位区域,转动转盘并启动角度识别系统,确定角度位置,停止转盘,完成1号工件的角度识别;
4、角度识别系统发出下料指令,机器人拿起1号工件,放入2号工件进行识别。转盘旋转,角度识别系统启动确定角度位置。转盘停止,2号工件角度识别完成,发出下料指令;
5、机器人接收1号立车下料指令,运动至1号立车上下料位进行下料上料,该动作完成后,立车单件加工循环开始;
6、机器人将1号立车加工完毕的成品取走,放置到工件翻转台1号位置;
7、机械手接收到2号立车下料指令,运动至2号立车上下料位进行下料上料,完成动作,开始立车单件加工循环;
8、机器人将2号立车加工完毕的成品取走,放置到工件翻转台的2号位置;
9、机器人等待立式加工的下料命令;
10、立式加工发出下料指令,机器人运动至立式加工上下料位,分别抓取并移动1号、2号工位的工件至下料托盘上,并将工件分别放置于托盘上;机器人运动至翻转台,分别抓取并送入1号、2号工件至立式加工上下料位,并将1号、2号工件分别放置于液压夹具1号、2号工位的定位区域内,完成立式加工上料。机器人移出立式加工安全距离,开始单次加工循环;
11、机器人运动至1号载料盘,准备启动二次循环程序;
描述:
1、机器人取料托盘上的16件(一层),机器人将吸盘夹钳更换,并将隔板放入暂存篮内;
2、机器人将16件(一层)装在下料托盘上,机器人要更换一次吸盘钳,将隔板放在从暂存篮中取出的零件的隔断面上;
3、根据检查频率,确保机器人将零件放置在手动取样台上;
1 | 加工周期时间表 | ||||||||||||||
2 | 顾客 | 工件材料 | QT450-10-GB/T1348 | 机床型号 | 档案编号 | ||||||||||
3 | 产品名称 | 117 轴承座 | 图号 | DZ90129320117 | 准备日期 | 2020.01.04 | 编制 | ||||||||
4 | 工艺步骤 | 刀号 | 加工内容 | 工具名称 | 切割直径 | 切割速度 | 转速 | 每转进给 | 机床进给 | 扦插次数 | 每个过程 | 加工时间 | 空闲时间 | 四轴旋转时间 | 换刀时间 |
5 | 不。 | 不。 | 解说 | 工具 | D 毫米 | n | 转速 | 毫米/转 | 毫米/分钟 | 时代 | mm | 秒 | 秒 | 秒 | |
6 | ![]() | ||||||||||||||
7 | 1 | T01 | 铣削安装孔表面 | 40面铣刀直径 | 40.00 | 180 | 1433 | 1.00 | 1433 | 8 | 40.0 | 13.40 | 8 | 4 | |
8 | 钻直径 17 的安装孔 | 直径17组合钻 | 17.00 | 100 | 1873 | 0.25 | 468 | 8 | 32.0 | 32.80 | 8 | 4 | |||
9 | T03 | DIA17孔背倒角 | 反向倒角刀 | 16.00 | 150 | 2986 | 0.30 | 896 | 8 | 30.0 | 16.08 | 16 | 4 | ||
10 | 描述: | 切割时间: | 62 | 第二 | 夹具装夹及上料下料时间: | 30.00 | 第二 | ||||||||
11 | 辅助时间: | 44 | 第二 | 总加工工时: | 136.27 | 第二 |
1 | 加工周期时间表 | |||||||||||||||||
2 | 顾客 | 工件材料 | QT450-10-GB/T1348 | 机床型号 | 档案编号 | |||||||||||||
3 | 产品名称 | 118轴承座 | 图号 | DZ90129320118 | 准备日期 | 2020.01.04 | 编制 | |||||||||||
4 | 工艺步骤 | 刀号 | 加工内容 | 工具名称 | 切割直径 | 切割速度 | 转速 | 每转进给 | 机床进给 | 扦插次数 | 每个过程 | 加工时间 | 空闲时间 | 四轴旋转时间 | 换刀时间 | |||
5 | 不。 | 不。 | 解说 | 工具 | D 毫米 | n | 转速 | 毫米/转 | 毫米/分钟 | 时代 | mm | 秒 | 秒 | 秒 | ||||
6 | ![]() | |||||||||||||||||
7 | 1 | T01 | 铣削安装孔表面 | 40面铣刀直径 | 40.00 | 180 | 1433 | 1.00 | 1433 | 8 | 40.0 | 13.40 | 8 | 4 | ||||
8 | T02 | 钻直径 17 的安装孔 | 直径17组合钻 | 17.00 | 100 | 1873 | 0.25 | 468 | 8 | 32.0 | 32.80 | 8 | 4 | |||||
9 | T03 | DIA17孔背倒角 | 反向倒角刀 | 16.00 | 150 | 2986 | 0.30 | 896 | 8 | 30.0 | 16.08 | 16 | 4 | |||||
10 | 描述: | 切割时间: | 62 | 第二 | 夹具装夹及上料下料时间: | 30.00 | 第二 | |||||||||||
11 | 辅助时间: | 44 | 第二 | 总加工工时: | 136.27 | 第二 | ||||||||||||
12 |
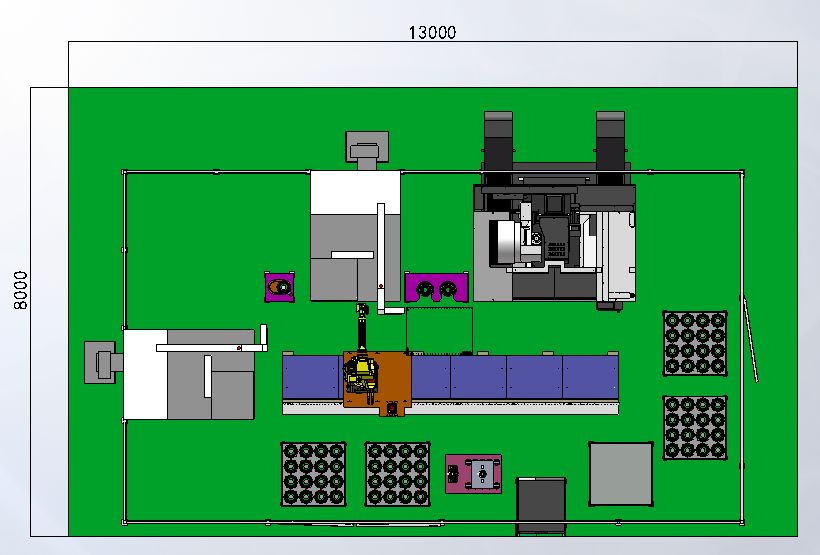
生产线覆盖面积
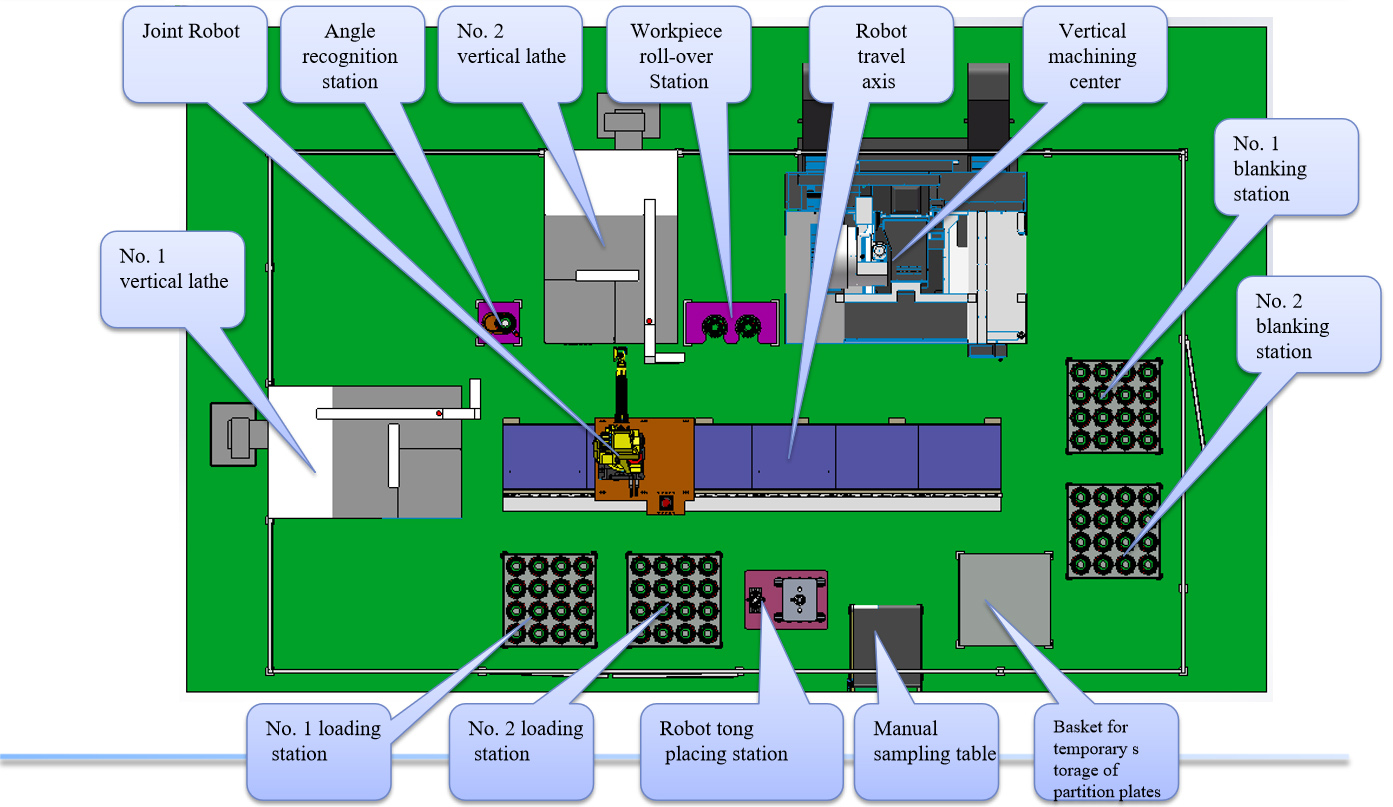
生产线主要功能部件介绍
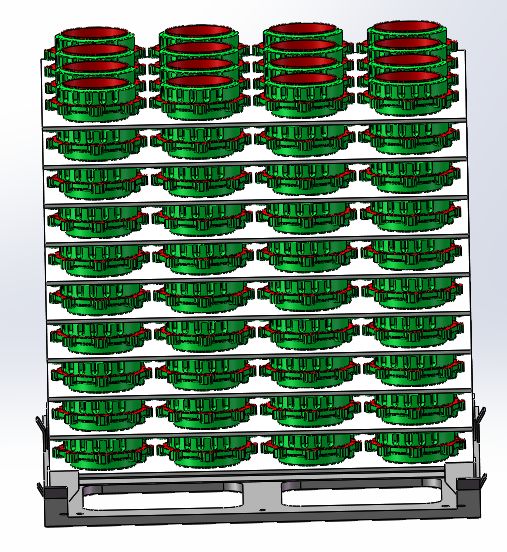
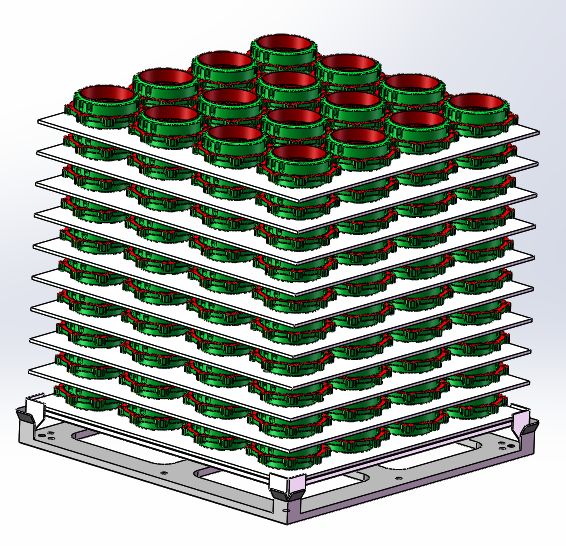
引入上下料系统
本方案自动化生产线存储设备为:堆垛托盘(每个托盘装箱件数与客户协商),提供工件毛坯3D图或实物后确定工件在托盘中的定位。
1、工人将粗加工好的零件装在料盘上(如图所示),用叉车搬运到指定位置;
2、叉车更换托盘后,手动按键确认;
3、机器人抓取工件进行上料工作;
机器人行走轴介绍
该结构由关节机器人、伺服电机驱动、齿轮齿条传动组成,使机器人能够进行往复直线运动,实现一台机器人服务多台机床、多工位抓取工件的功能,提高关节机器人的工作覆盖率;
行走轨道采用钢管焊接底座,采用伺服电机、齿轮齿条传动,增大关节机器人的工作覆盖范围,有效提高机器人的利用率;行走轨道安装在地面上;
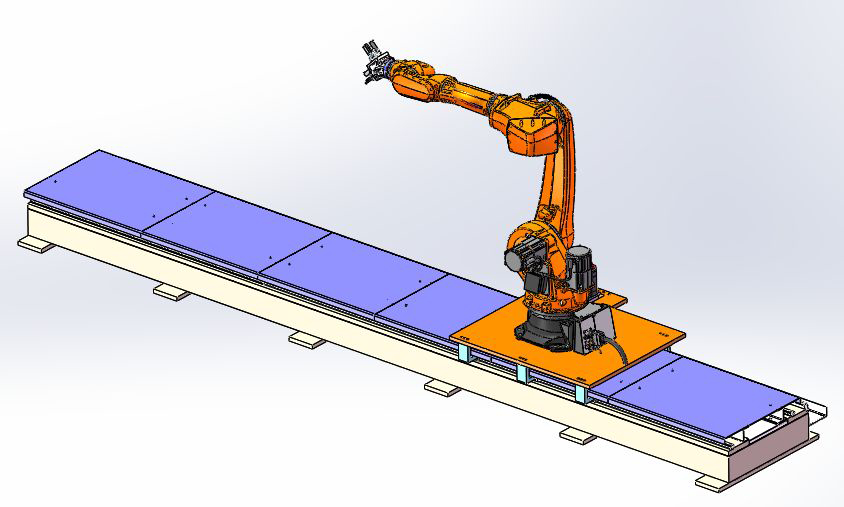
辰轩机器人:SDCX-RB500
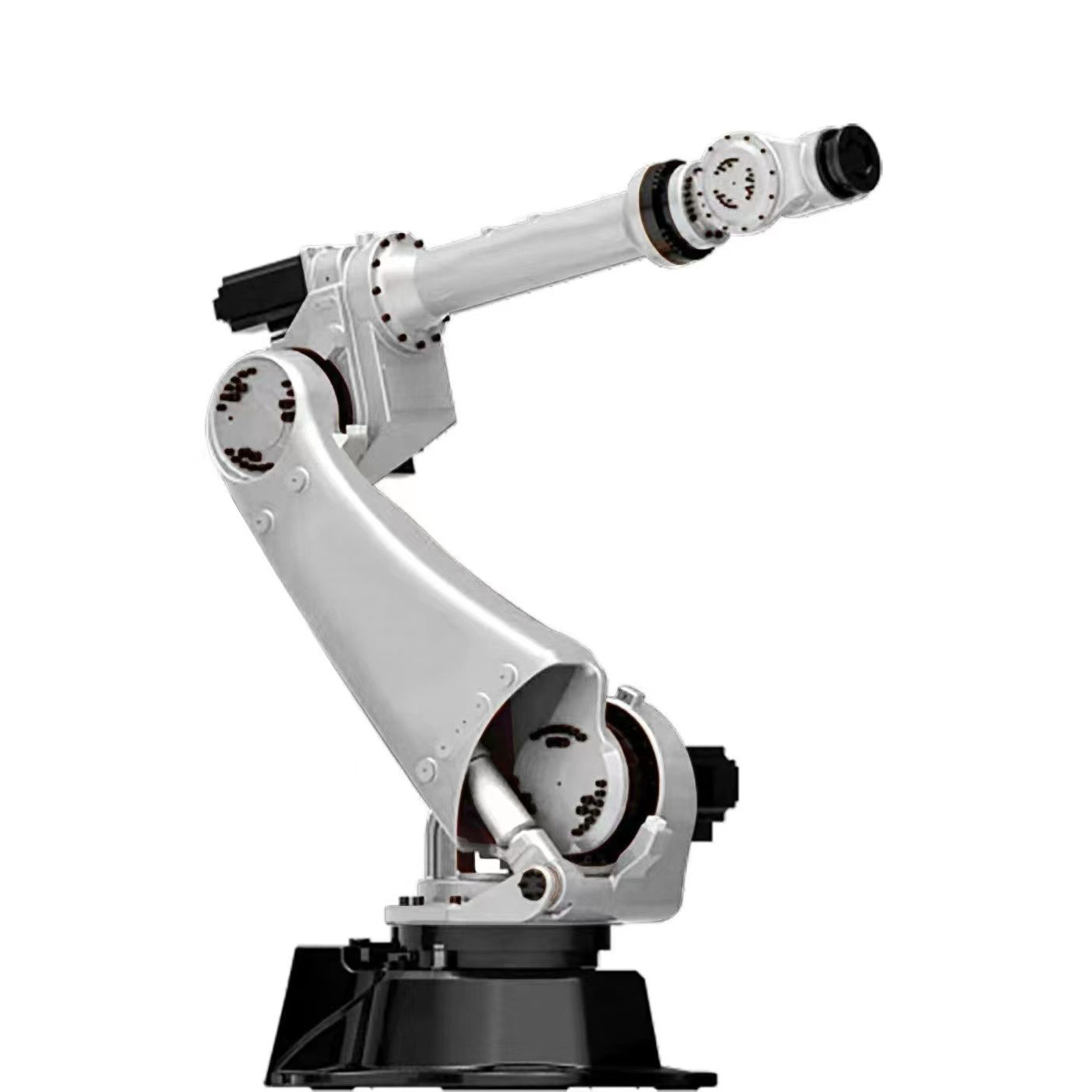
基本数据 | |
类型 | SDCX-RB500 |
轴数 | 6 |
最大覆盖范围 | 2101毫米 |
姿势重复性(ISO 9283) | ±0.05毫米 |
重量 | 553公斤 |
机器人防护等级 | 防护等级,IP65 / IP67直列手腕(IEC 60529) |
安装位置 | 天花板,允许倾斜角度≤0º |
表面处理、油漆 | 底座框架:黑色(RAL 9005) |
环境温度 | |
手术 | 283 K 至 328 K(0 °C 至 +55 °C) |
储存和运输 | 233 K 至 333 K(-40 °C 至 +60 °C) |
机器人后部和底部拥有广阔的运动范围,可采用天花板升降安装。由于机器人横向宽度被压缩到极限,因此可以紧密贴合相邻的机器人、夹具或工件进行安装。可从待机位置高速移动到作业位置,并在短距离移动中快速定位。
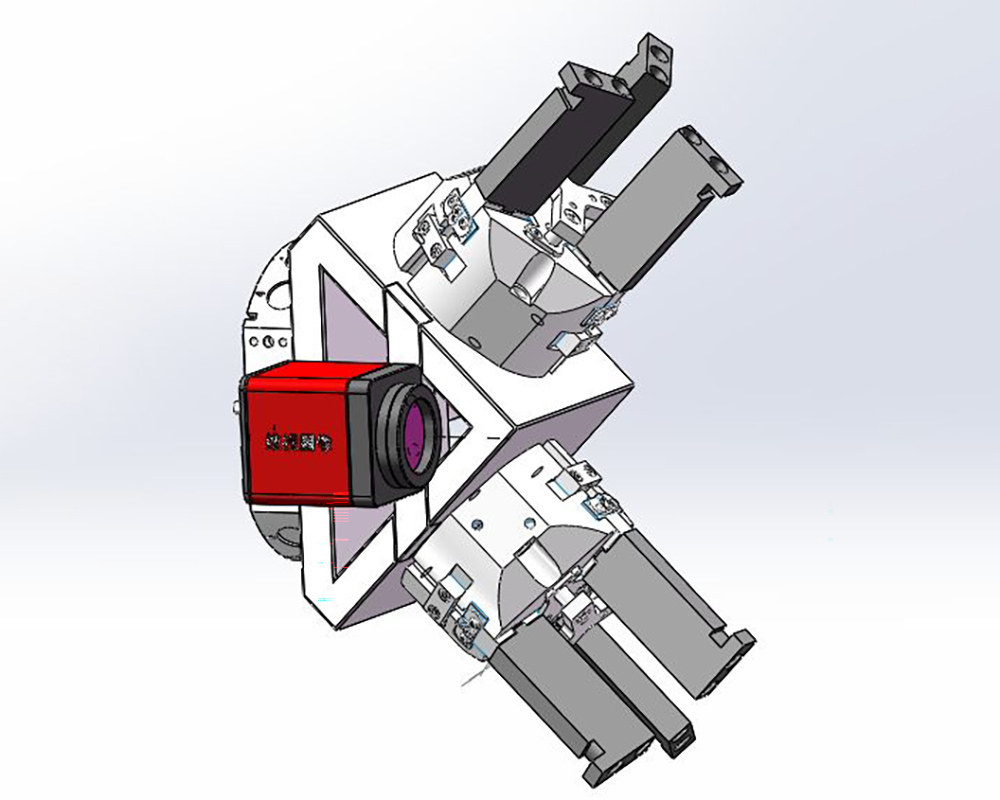
智能机器人上下料钳机构
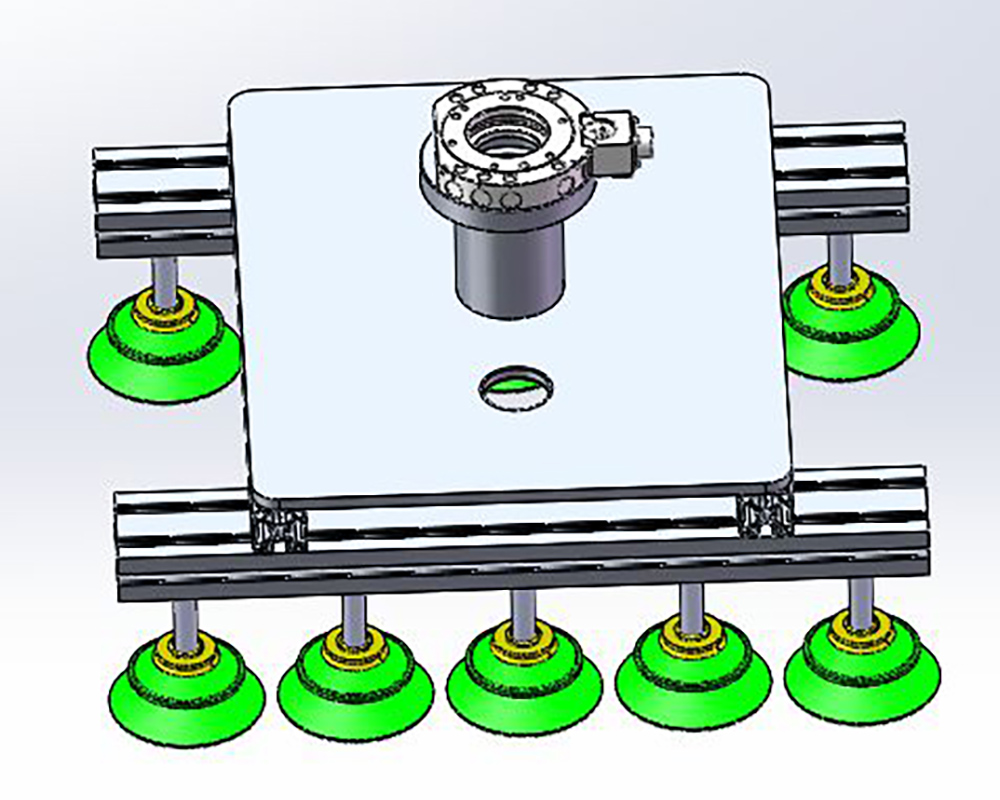
机器人隔板夹钳机构
描述:
1、针对该零件的特点,采用三爪外支撑方式上下料,可实现该零件在机床上的快速车削;
2、机构设有位置检测传感器和压力传感器,检测零件夹紧状态和压力是否正常;
3、机构设有加压装置,在停电、主气路断气的情况下,工件不会在短时间内脱落;
4、采用手动换钳装置,更换夹钳机构可快速完成不同材料的夹持。
换钳装置介绍
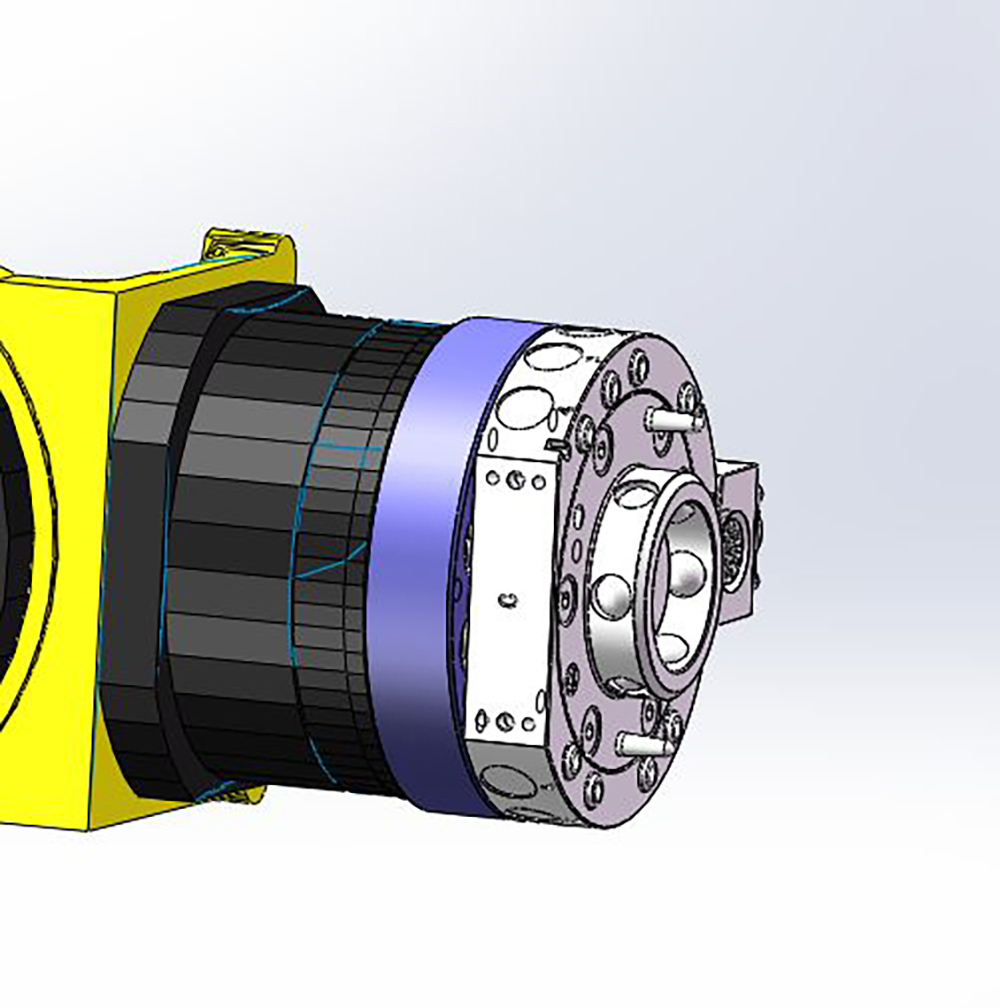
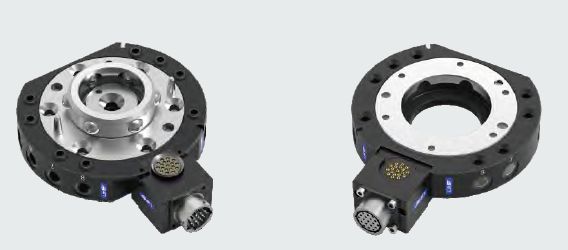
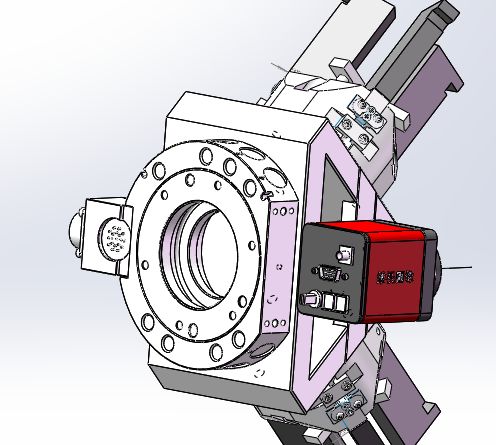
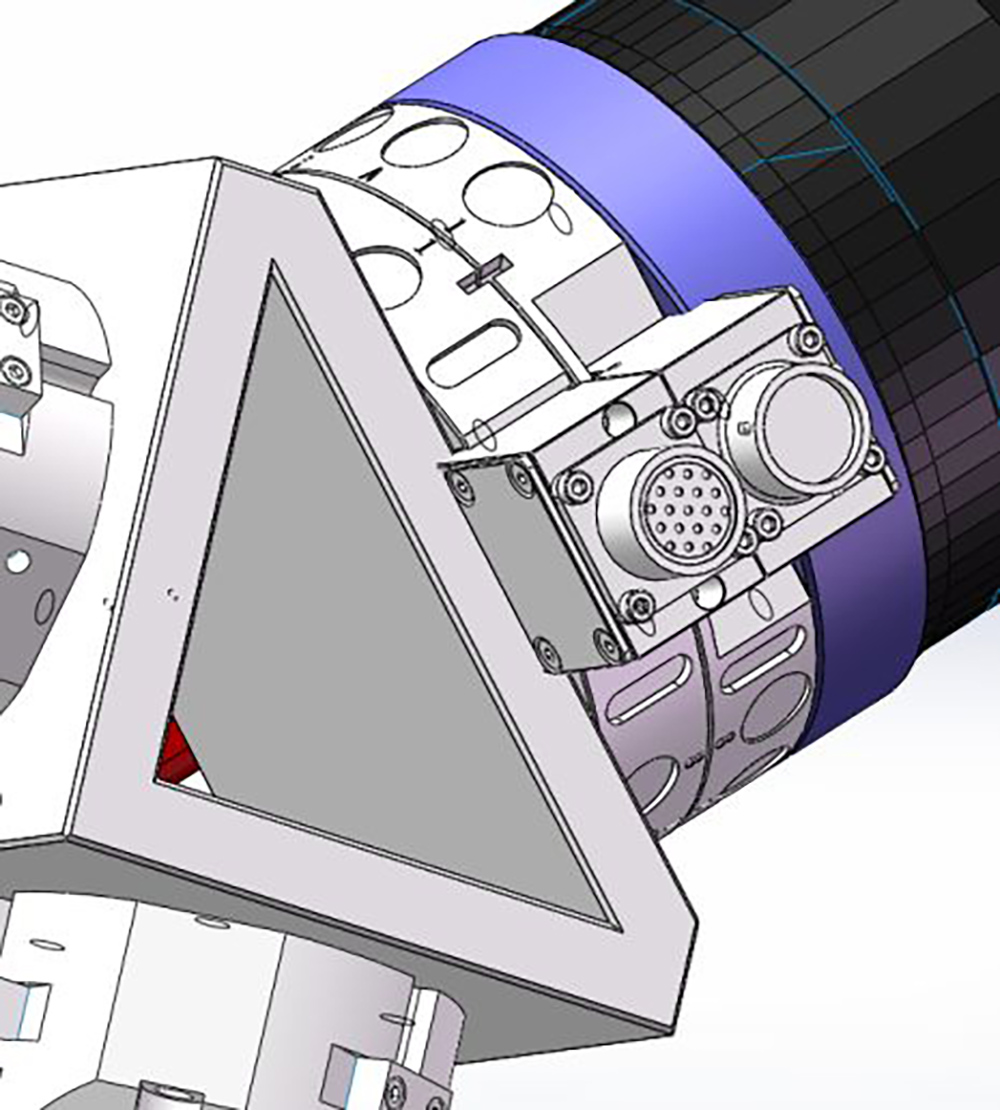
精密夹钳更换装置用于快速更换机器人夹钳、工具端及其他执行机构。减少生产闲置时间,提高机器人灵活性,其特点如下:
1.解锁并拧紧气压;
2、可采用多种动力、液体、气体模块;
3、标准配置可快速与气源连接;
4、特设保险机构,可防止意外断气的风险;
5.无弹簧反作用力;6.适用于自动化领域;
视觉系统简介-工业相机
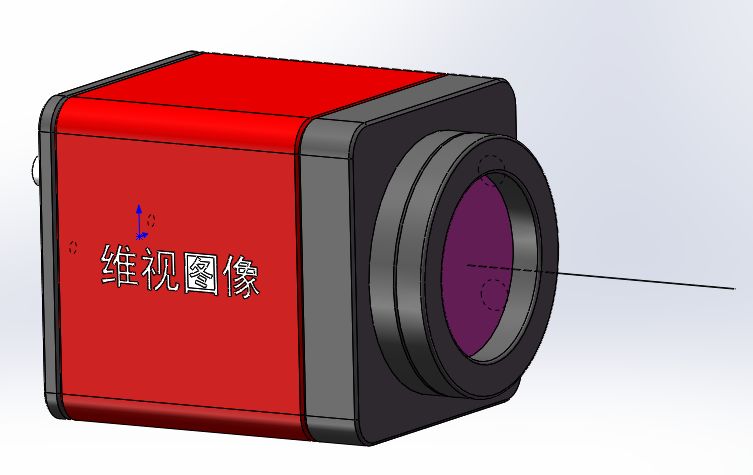
1、摄像机采用高品质CCD和CMDS芯片,具有高分辨率、高灵敏度、高信频比、宽动态范围、成像质量优良、色彩还原能力一流的特点;
2、面阵相机有两种数据传输方式:千兆以太网(GigE)接口、USB3.0接口;
3.相机结构紧凑,外形小巧,重量轻,安装简便。传输速度快,抗干扰能力强,输出高质量图像稳定;适用于读码、缺陷检测、DCR、图案识别等;彩色相机色彩还原能力强,适用于对色彩识别要求较高的场景;
角度自动识别系统介绍
功能介绍
1、机器人从上料篮中夹取工件,并送至转盘定位区域;
2、转盘在伺服电机的驱动下旋转;
3、视觉系统(工业相机)工作,识别角度位置,转台停止,确定所需角度位置;
4、机器人取出工件,放入另一件工件进行角度识别;
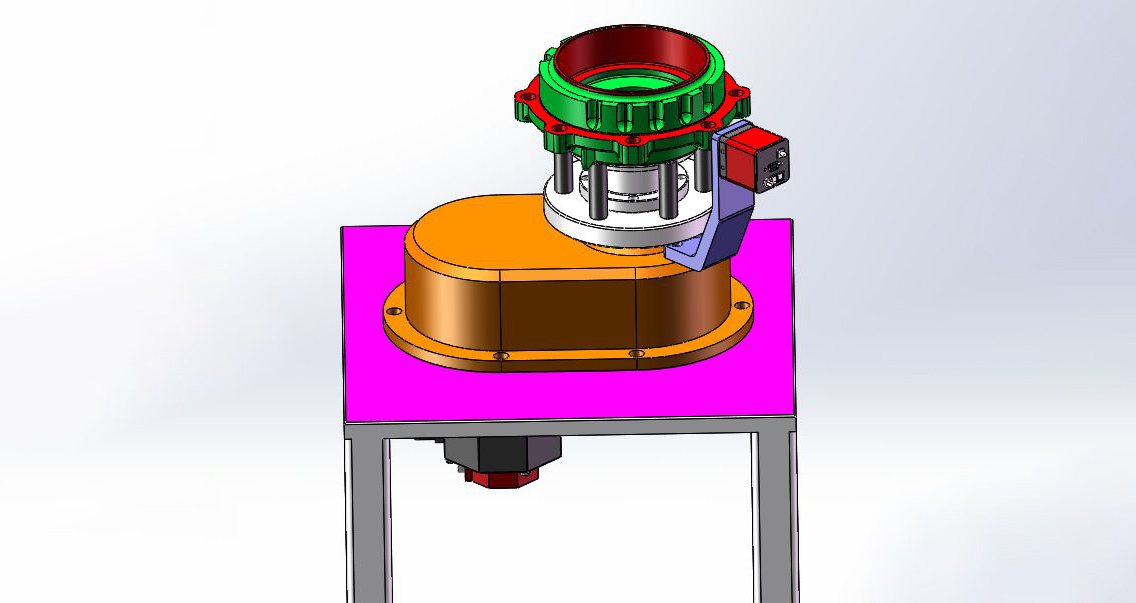
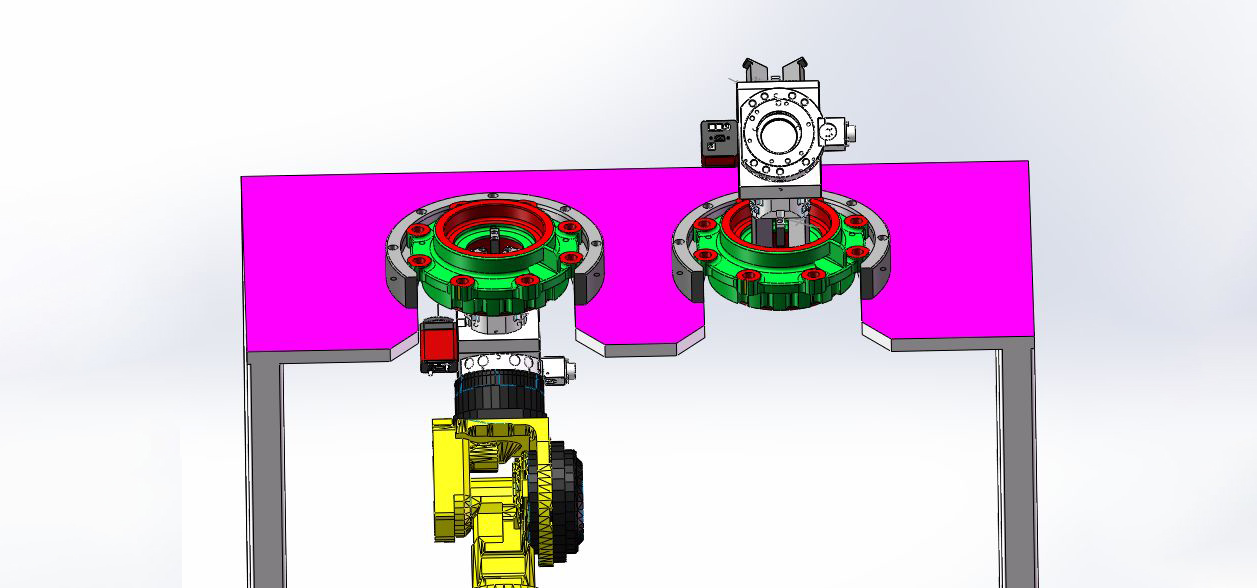
工件翻转台简介
翻车站:
1、机器人拿起工件,放置到翻转台的定位区域(图中左侧工位);
2、机器人从上方抓取工件,实现工件的翻转;
机器人夹钳放置台
功能介绍
1、每层零件装载完毕后,应将分层隔板放入隔板暂存篮内;
2、机器人可通过换钳装置快速更换吸盘钳,并可拆除隔板;
3、隔板摆放好后,取下吸盘钳,换上气动钳,继续上料、下料;
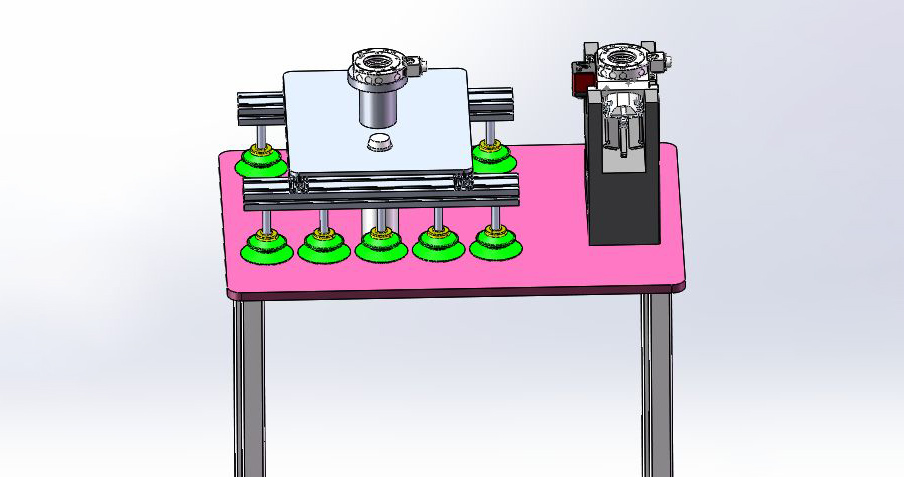
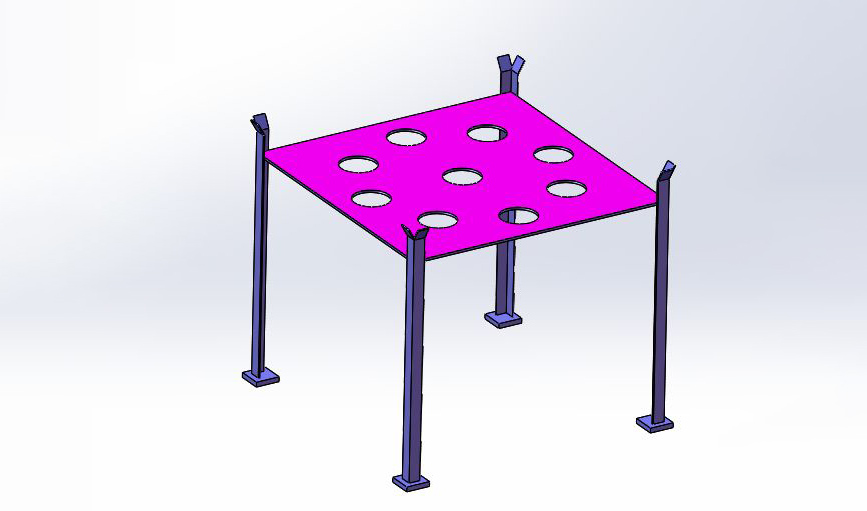
隔板临时存放篮
功能介绍
1、设计规划一个隔板临时筐,先撤掉上料隔板,再使用下料隔板;
2、上车隔板人工摆放,一致性差,将隔板放入暂存筐后,机器人才能取出并整齐摆放;
手动采样表
描述:
1、针对不同的生产阶段设定不同的人工随机采样频率,可有效监督在线测量的有效性;
2、使用说明:机械手按照手动设定的频率将工件放置到采样台的设定位置,并以红灯提示。检测人员按按钮将工件运送到防护外的安全区域,测量完毕后取出工件进行测量并单独存放;
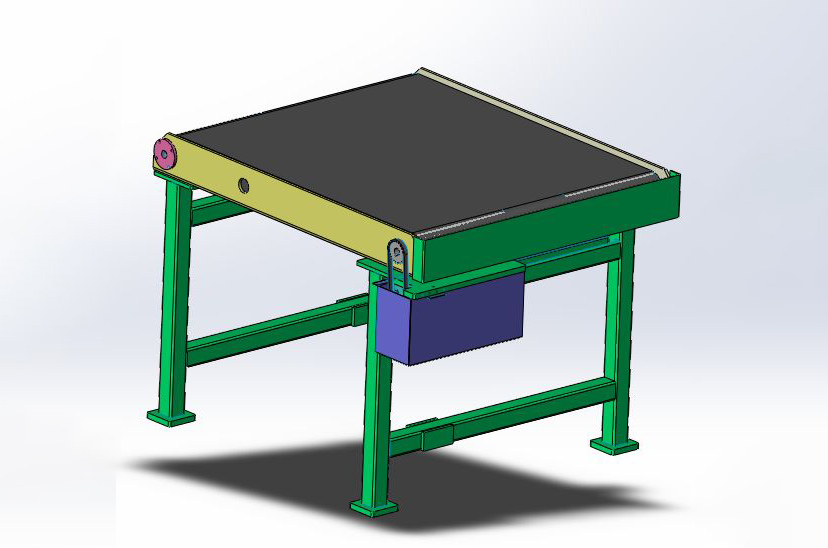
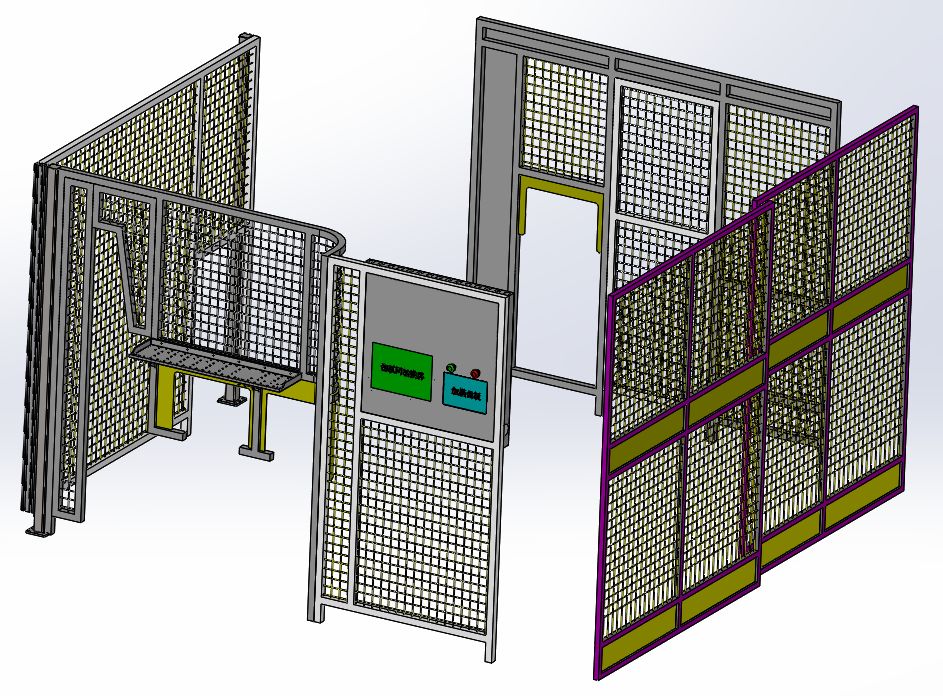
保护元件
采用轻质铝型材(40×40)+网片(50×50)构成,触摸屏、急停按钮可集成到防护部件上,集安全性与美观性于一体。
OP20液压夹具介绍
处理说明:
1、以φ165内孔为基孔,以D基准为基面,以两安装孔凸台外圆弧为角度限位;
2、通过机床M指令控制压板的松开、压紧动作,完成安装孔凸台上平面、8-φ17安装孔及孔两端的倒角加工;
3、夹具具有定位、自动夹紧、气密性检测、自动松开、自动顶出、自动冲屑、自动清洁定位基准面等功能;
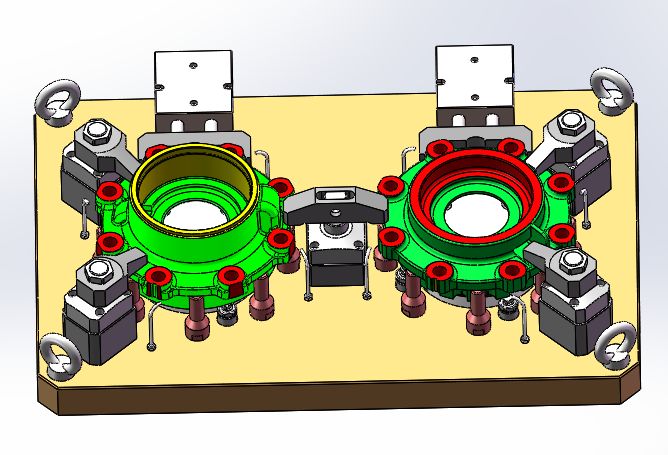
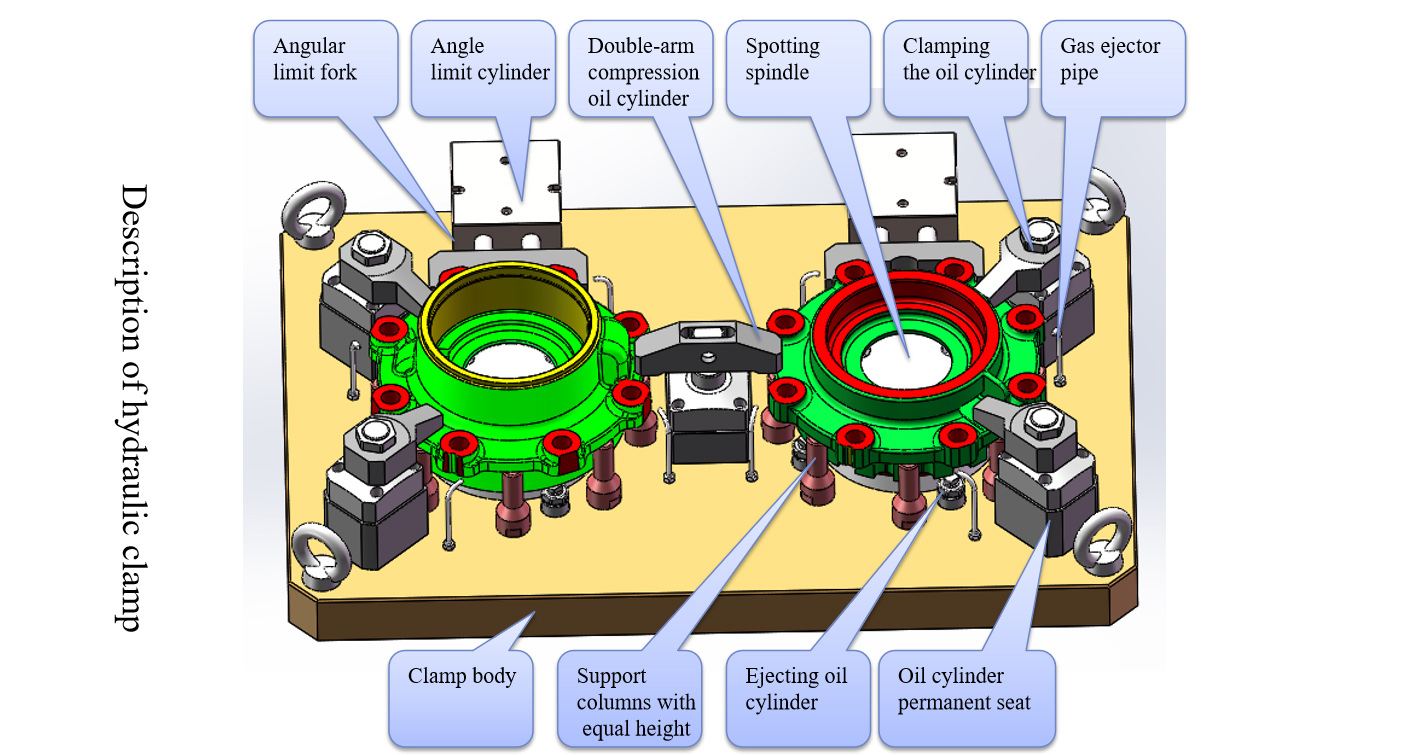
生产线设备要求
1、生产线设备夹具具备自动夹紧、松开功能,在机械手系统信号的控制下,实现自动夹紧、松开功能,配合上下料动作;
2、生产线设备钣金件需预留天窗位置或自动门模块,以配合我司电控信号及机械手通讯;
3、产线设备通过重载连接器(或航空插头)的连接方式与机械手通讯;
4、生产线设备内部(干扰)空间大于机械手钳口动作的安全范围;
5、生产线设备应保证夹具定位面无残留铁屑,必要时应加大吹气清理(清理时卡盘应旋转);
6、生产线设备断屑良好,必要时可增设我公司辅助高压断屑装置;
7、当生产线设备要求机床主轴准确停止时,增加此功能并提供相应电气信号;
立式车床VTC-W9035介绍
VTC-W9035数控立式车床适用于加工齿轮毛坯、法兰、异形壳体等旋转体零件,尤其适用于盘类、轮毂、刹车盘、泵体、阀体、壳体等零件的精密、省力、高效车削。机床具有整体刚性好、精度高、单位时间金属去除率大、精度保持性好、可靠性高、维护方便等优点,应用范围广泛,可实现流水线生产,效率高,成本低。
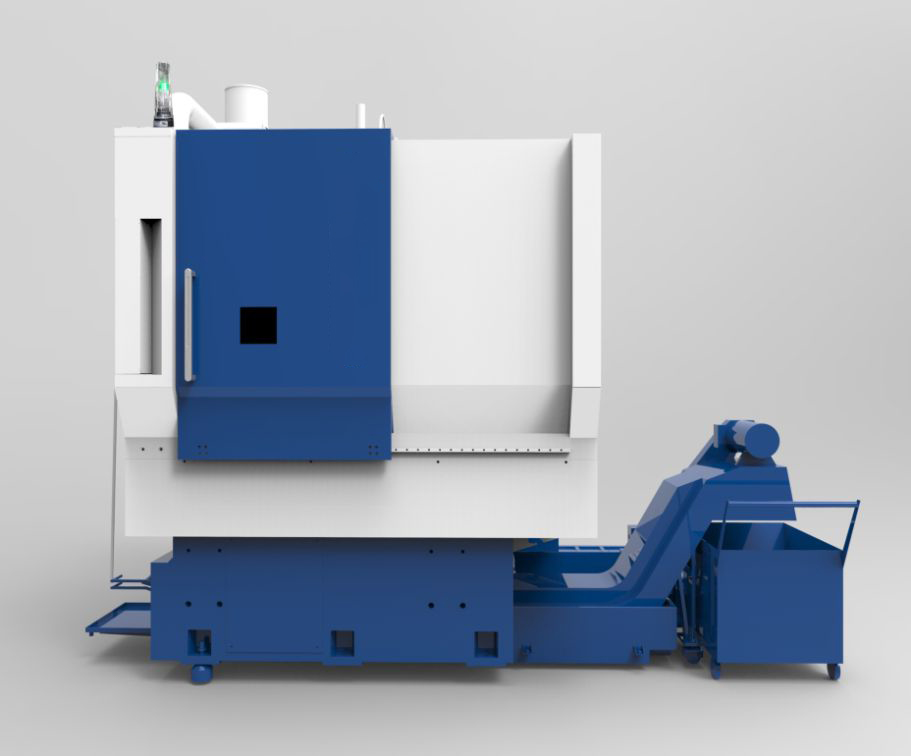
模型类型 | VTC-W9035 |
床身最大回转直径 | φ900毫米 |
滑板最大回转直径 | φ590毫米 |
工件最大回转直径 | φ850毫米 |
工件最大车削长度 | 700毫米 |
主轴转速范围 | 20-900转/分 |
系统 | FANUC 0i-TF |
X/Z轴最大行程 | 600/800 毫米 |
X/Z轴快速移动速度 | 20/20米/分钟 |
机床长、宽、高 | 3550*2200*3950毫米 |
项目 | 单元 | 范围 | |
加工范围 | X轴行程 | mm | 1100 |
X轴行程 | mm | 610 | |
X轴行程 | mm | 610 | |
主轴鼻端至工作台距离 | mm | 150~760 | |
工作台 | 工作台尺寸 | mm | 1200×600 |
工作台最大承重 | kg | 1000 | |
T型槽(尺寸×数量×间距) | mm | 18×5×100 | |
喂食 | X/Y/Z轴进给速度快 | 米/分钟 | 36/36/24 |
主轴 | 驾驶模式 | 皮带类型 | |
主轴锥度 | BT40 | ||
最大运行速度 | 转/分 | 8000 | |
功率(额定/最大) | KW | 11/18.5 | |
扭矩(额定/最大) | 牛·米 | 52.5/118 | |
准确性 | X/Y/Z轴定位精度(半闭环) | mm | 0.008(总长度) |
X/Y/Z轴重复精度(半闭环) | mm | 0.005(总长度) | |
刀库 | 类型 | 光盘 | |
刀库容量 | 24 | ||
最大刀具尺寸(全刀具直径/空相邻刀具直径/长度) | mm | Φ78/Φ150/300 | |
最大刀具重量 | kg | 8 | |
各种各样的 | 供气压力 | 兆帕 | 0.65 |
电源容量 | 千伏安 | 25 | |
机床外形尺寸(长×宽×高) | mm | 2900×2800×3200 | |
机床重量 | kg | 7000 |
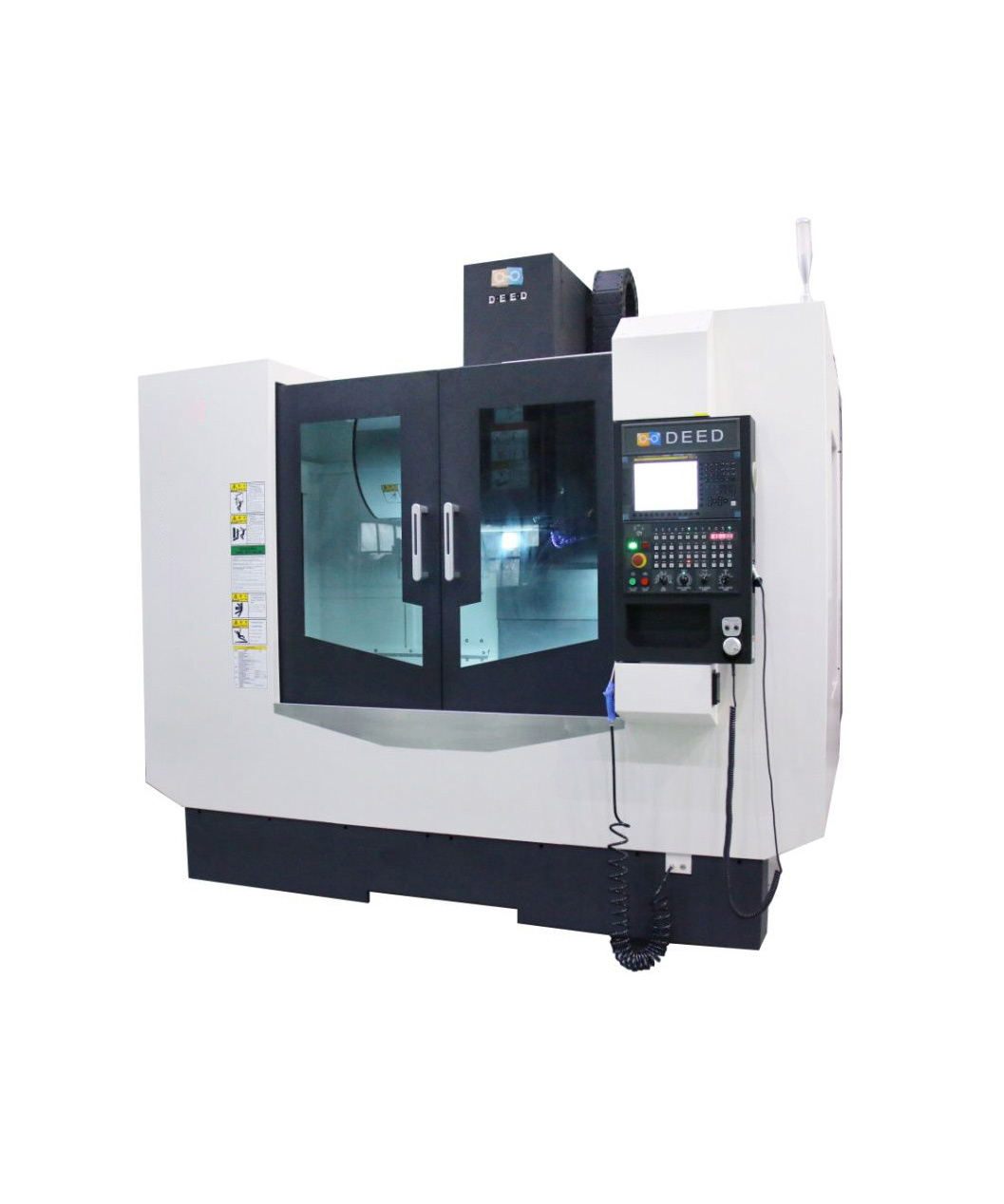